The Complete Guide to Teflon™ Coating
Published July 2025

Introduction
In today’s industrial world, efficiency, durability, and cleanliness are non-negotiable, especially in sectors like packaging, where machine performance directly impacts product quality and uptime. One of the most effective ways to boost all three is through Teflon coating.
Teflon coating has long been known for its exceptional non-stick properties, but in the packaging industry and beyond, its value goes far deeper. From increasing the lifespan of equipment like non-stick coating to seal bars to improving safety and reducing maintenance downtime, Teflon coating for packaging machinery, industrial equipment, and high heat applications are a game-changer for any operation that values consistency and reliability.
In this guide, we’ll walk you through everything you need to know about Teflon coating: what it is, why it’s used, its benefits, and how we deliver industry-leading results with our custom PTFE coating solutions. We’ll also break down its safety, the industries it serves, and what sets our process apart from the competition.
Whether you’re exploring Teflon coating for the first time or looking to improve your packaging process, you can find the answers here.
What is Teflon Coating?
Teflon coating, commonly referred to as PTFE Teflon coating, is a high-performance, non-stick, and heat-resistant surface treatment used across many industrial applications. At its core, Teflon is the brand name for PTFE (Polytetrafluoroethylene), a synthetic fluoropolymer known for its durability, slickness, and resistance to extreme environments.
At Inter-Tech Supplies, we only provide PTFE Teflon coating to ensure high-quality and high durability to improve parts, components, seal plates, forming heads, and really anything that needs it. Our custom Teflon coating services are trusted by packaging and manufacturing clients who require reliable, high-temperature protection and easy-clean surfaces. We have Teflon coated machine parts for manufacturing, baking sheets for bakeries, butterfly valves for plumbing companies, and more. Our custom Teflon coating services are limitless with the proper dimensions.
Types of Teflon Coating:
- PTFE (Polytetrafluoroethylene): The most common type, offering excellent non-stick and heat resistance. This is the type of coating we offer.
- FEP (Fluorinated Ethylene Propylene): Offers more flexibility and transparency, ideal for chemical resistance.
- PFA (Perfluoroalkoxy): More resistant to cracking under stress and heat.
- ETFE (Ethylene Tetrafluoroethylene): Highly durable and impact-resistant, often used in architectural and aerospace settings.
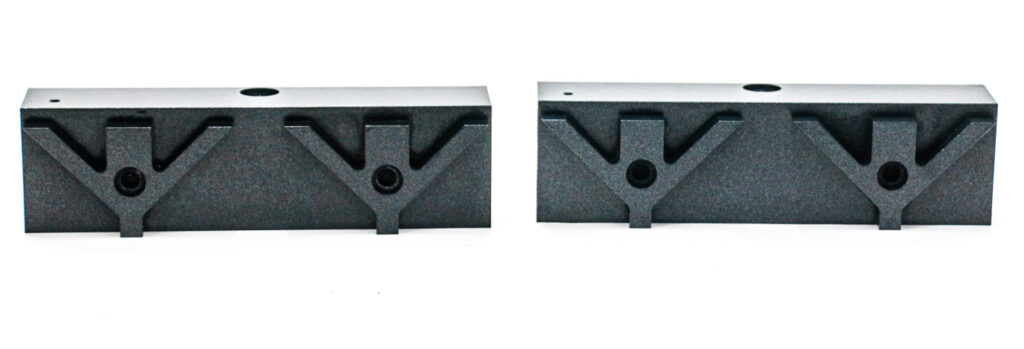
How Teflon Works
Teflon’s magic lies in its low surface energy and high molecular stability. These properties allow it to repel water, resist sticking to most materials, and stand up to extreme temperatures and corrosive chemicals.
Industrial Application
In packaging machinery, Teflon coating is commonly applied to parts like sealing and forming die heads, seal plates, trays, guide rails, blades, seal bars, and rollers to reduce friction, prevent build-up, and extend service life.
We have also coated other industries than just packaging equipment in the past as well, including baking sheets, butterfly valves, and pizza trays. Check out examples of our previous work on our Teflon Services page or on our LinkedIn account.
Benefits of Teflon Coating
Teflon coating isn’t just about making surfaces slippery. It’s a performance enhancing upgrade that delivers measurable results across a wide range of manufacturing and packaging environments. Here’s why Teflon coating has become a must-have in packaging machinery, food processing applications, and all other modern industrial operations.
1. Non-Stick Properties
One of Teflon’s most well-known characteristics is its non-stick surface. In packaging equipment, this means materials like adhesives, films, and product residues don’t cling to components, reducing downtime caused by cleaning or build-up.
Example: Sealing die heads coated with Teflon won’t accumulate melted film or product overflow, keeping production lines cleaner and faster and reducing downtimes.
2. High Heat Resistance
Teflon coatings can withstand continuous temperatures up to 260°C (500°F), making them ideal for high-heat processes like sealing, cutting, or thermal bonding. This thermal stability ensures performance and safety even under intense operating conditions.
3. Chemical Resistance
Teflon is inert to most chemicals, acids, and solvents. This makes it especially useful in packaging lines that deal with caustic cleaning agents, wash downs, volatile products, or harsh production environments.
4. Reduced Wear and Friction
Teflon-coated surfaces are smoother and produce less friction, which minimizes mechanical wear on moving parts. This results in:
- Less frequent part replacement
- Lower lubrication requirements
- Longer machine uptime
- Less downtime needed
5. Corrosion Protection
Metal components coated with Teflon are protected against oxidation and corrosion, even in moist or chemically aggressive environments. This is crucial for maintaining equipment integrity and performance over time.
6. Lower Maintenance Costs
All the above benefits translate into reduced maintenance time, fewer repairs, and a longer lifespan for machine parts. Ultimately, Teflon coating for packaging machinery and equipment helps save you both time and money. PTFE Teflon coating helps your equipment work smarter, longer, and cleaner.
Why the Packaging Industry Should Use Teflon Coating
The packaging industry thrives on speed, precision, and cleanliness. Whether it’s shrink wrapping, sealing, cutting, thermoforming, or conveying, any inefficiency or contamination can cost time, money, and product integrity. Teflon coating, especially PTFE Teflon coating, directly addresses these challenges, making it a strategic asset for packaging manufacturers.
1. Reduces Downtime and Cleaning Requirements
Packaging lines can experience frequent interruptions due to material build-up, heat-induced sticking, or gumming on machine parts. How Teflon coating works on packaging equipment is due to it’s non-stick and heat-resistant nature that keeps the parts and machinery clean and operating smoothly, which:
- Reduces manual cleaning time
- Minimizes stoppages for part replacement or maintenance
- Keeps production consistent and on schedule
2. Improves Product Quality and Safety
When packaging machine components accumulate residue or wear out, it can lead to product contamination or inconsistent seals. Teflon’s smooth, non-reactive surface prevents unwanted material transfer and helps ensure a hygienic, high-quality final product.
3. Boosts Operational Efficiency
By reducing friction and wear, PTFE Teflon coated parts allow machinery to run at higher speeds with less strain. PTFE Teflon coated parts become more durable and resistant to heat and chemicals and that means:
- Fewer breakdowns
- Smoother product flow
- Longer service intervals
4. Extends Equipment Lifespan
Teflon acts as a protective barrier, shielding metal parts from heat, moisture, chemicals, and abrasion. This protection significantly prolongs the life of expensive components like sealing bars, guide rails, seal plates, and custom blades.
5. Offers Long-Term Cost Savings
While the initial cost of coating might be higher than untreated components, the long-term savings are substantial. Reduced part replacements, fewer service calls, and less downtime all contribute to a better bottom line.
In short: For packaging lines looking to scale up productivity while maintaining cleanliness and quality, Teflon coating is not a luxury, it’s a smart investment.
Is Teflon Coating Safe?
Teflon has been the subject of safety questions over the years, especially in relation to cookware. But when it comes to industrial and packaging applications, the conversation shifts significantly. Used correctly, Teflon coating is not only safe, it’s a certified, industry-trusted solution for improving machinery performance without compromising health or safety.
Understanding the Concerns
Most public concerns around Teflon stem from earlier issues with a chemical called PFOA (Perfluorooctanoic Acid), which was used in Teflon production in the past. However:
- PFOA was phased out by major manufacturers by 2013.
- Today’s industrial Teflon coatings are PFOA-free and compliant with safety standards.
Safe When Applied and Used Properly
In industrial settings, Teflon is applied by trained professionals in controlled environments and cured at high temperatures. Once cured:
- The coating is stable, inert, and non-reactive.
- It doesn’t emit harmful substances during normal use.
- It poses no health hazard to workers, consumers, or end-users of packaged products.
Teflon and Heat: What You Should Know
While Teflon can degrade at extreme temperatures (above 500°F or 260°C), packaging equipment typically operates within safe temperature limits. When used properly, there is no risk of off-gassing or breakdown.
Summary: Teflon coating, especially modern, industrial-grade formulations, is safe, stable, and trusted by top manufacturers in food, medical, and consumer goods industries.
Industries That Benefit from Teflon Coating
Teflon coatings aren’t just limited to one niche and one industry. It’s versatility makes them a go-to solution across multiple industries. From high-speed production lines to cleanroom environments, Teflon helps protect machinery, improve operations, and meet strict compliance standards.
Here’s a look at the industries that benefit most from this powerful coating:
1. Packaging Industry
Whether it’s food, pharmaceutical, cosmetic, or consumer goods packaging, PTFE Teflon coating plays a critical role in:
- Preventing material build-up on sealing heads, forming dies, seal bars, and other packaging components.
- Allowing high-temperature operation without damage.
- Reducing friction and wear on and increasing the durability of moving parts.



Result: Faster lines, less downtime, and more reliable sealing integrity.
2. Food & Beverage
FDA-compliant Teflon coatings are ideal for equipment that comes into direct or indirect contact with food. Whether that is baking trays or personal cookware, PTFE Teflon coating:
- Prevents sticking and contamination
- Withstands aggressive cleaning chemicals
- Ensures compliance with safety and hygiene standards
3. Medical & Pharmaceutical
Cleanliness and chemical resistance are key in the medical industry. Teflon helps by:
- Providing a non-stick, non-reactive surface on dosing and sealing equipment
- Standing up to disinfectants and cleaning protocols
- Supporting sterile production environments
4. Industrial Manufacturing
From injection molds to cutting and forming tools, Teflon coatings:
- Reduce friction and wear
- Prevent buildup of sticky materials or lubricants
- Extend tool life and minimize maintenance needs
Bottom Line: If your operation involves heat, chemicals, movement, or cleanliness, the chances are Teflon has a role to play.
Our Teflon Coating Process
At Inter-Tech Supplies, we don’t just apply PTFE Teflon. We engineer coatings tailored to your equipment’s demands. Our process is designed for precision, performance, competitive pricing, and long-term reliability. Whether you’re coating a single part, a seal plate, or an entire machine line, our PTFE Teflon coating experts are ready to help.
Here’s how we ensure the best results, every time:

Step 1: Consultation & Assessment
We start by understanding your application:
- What type of equipment are you coating?
- What operating conditions (temperature, friction, exposure) does it face?
- What are the dimensions of the equipment you need coated?
Step 2: Surface Preparation
Proper adhesion is critical, so we take prep seriously. This includes:
- Stripping old coatings (if needed)
- Sand blasting or etching for surface texture
- Thorough cleaning to remove oils or contaminants
This ensures maximum bonding strength and long-lasting durability for your packaging parts and machinery.
Step 3: Application
We use precision spray techniques and a 3-coat process to apply the PTFE Teflon evenly and accurately. Factors we control:
- Coating thickness (micron-level accuracy)
- Number of layers (single vs. multi-coat systems)
- Spray pattern and cure schedule
Each part is coated in a clean and controlled environment to eliminate defects.
Step 4: Curing
Once applied, the coating is cured in high-temperature ovens to chemically bond it to the substrate. Curing ensures:
- Full polymerization of the coating
- Maximum hardness, chemical resistance, and non-stick performance
- A smooth, durable, and uniform finish
Step 5: Inspection & Quality Control
Every coated part undergoes a final inspection, checking for:
- Uniform coverage
- Proper thickness
- Surface smoothness and adhesion
We only ship parts and components that meet our strict quality standards. No exceptions.
Why It Matters: Our detailed process ensures every coating we apply performs exactly as it should, even under the harshest industrial conditions. You get consistent, reliable results that protect your equipment and boost performance.
Want to see it for yourself? Check out our YouTube video detailing our process.
How Our Coating Compares to Competitors
Not all Teflon coatings, or coating providers, are created equal. At Inter-Tech Supplies, we go beyond the standard to deliver coatings that last longer, perform better, and are tailored to your operation’s exact needs. Here’s how we stack up against the competition:
1. Custom Engineering vs. One-Size-Fits-All
Others: Many providers use off-the-shelf coatings with minimal customization.
Inter-Tech Supplies: We tailor each coating to the specific equipment, temperature ranges, chemical exposure, and performance goals of your line.
Your parts aren’t generic — your coating shouldn’t be either.
2. Superior Surface Prep for Better Adhesion
Others: Skimp on blasting, cleaning, or use outdated prep methods.
Us: We follow rigorous preparation protocols to ensure maximum adhesion and long-term durability because a coating is only as good as the bond beneath it.
3. In-House Expertise
Others: Outsource coatings to third parties, adding delays and reducing quality control.
Inter-Tech Supplies: All coating services are handled in-house by trained specialists, so we maintain total control over quality, lead times, and performance.
4. Quality Control That Goes Deeper
Others: Rely on visual checks or skip post-coating testing altogether.
Us: We use precision tools to verify coating thickness, adhesion, surface finish, and every part gets inspected before it ships.
5. Seamless Integration With Other Services
As part of our broader packaging support, including replacement parts, molded silicone gaskets, laser cutting, and tooling repair/fabrication, we can handle coating as part of a complete parts package. That means:
- Faster turnaround
- Fewer vendors
- More consistent results
Bottom Line: We don’t just apply PTFE Teflon, we deliver performance coatings built to outlast and outperform the rest.
The Smart Choice for Smarter Packaging
Teflon coating is more than just a surface treatment, it’s a strategic advantage. Whether you’re trying to reduce maintenance, improve product quality, or extend the life of your equipment, Teflon delivers reliable performance across countless packaging and industrial applications.
At Inter-Tech Supplies, we don’t just Teflon coat parts, we solve problems, optimize production, and support your long-term success with coatings engineered for durability, safety, and efficiency.
Need a Quote or Want to Discuss Your Application?
We’re here to help. Contact us today to learn how we can improve your packaging line with custom-engineered PTFE Teflon solutions.
Let’s get your equipment running cleaner, faster, and longer.
100% In-House Design And Manufacturing!
We can create your gasket from a sample or a CAD drawing.